Exactly how to Determine What is Porosity in Welding and Improve Your Method
The Science Behind Porosity: A Comprehensive Guide for Welders and Fabricators
Comprehending the complex mechanisms behind porosity in welding is critical for welders and makers striving for impeccable workmanship. From the structure of the base products to the ins and outs of the welding procedure itself, a wide variety of variables conspire to either intensify or ease the visibility of porosity.
Understanding Porosity in Welding
FIRST SENTENCE:
Exam of porosity in welding discloses crucial understandings right into the honesty and quality of the weld joint. Porosity, identified by the visibility of dental caries or voids within the weld metal, is a typical concern in welding procedures. These voids, otherwise properly addressed, can endanger the architectural integrity and mechanical residential properties of the weld, bring about possible failings in the ended up item.

To find and evaluate porosity, non-destructive screening approaches such as ultrasonic screening or X-ray evaluation are typically used. These methods permit the recognition of inner flaws without jeopardizing the honesty of the weld. By assessing the dimension, shape, and distribution of porosity within a weld, welders can make educated decisions to enhance their welding procedures and accomplish sounder weld joints.
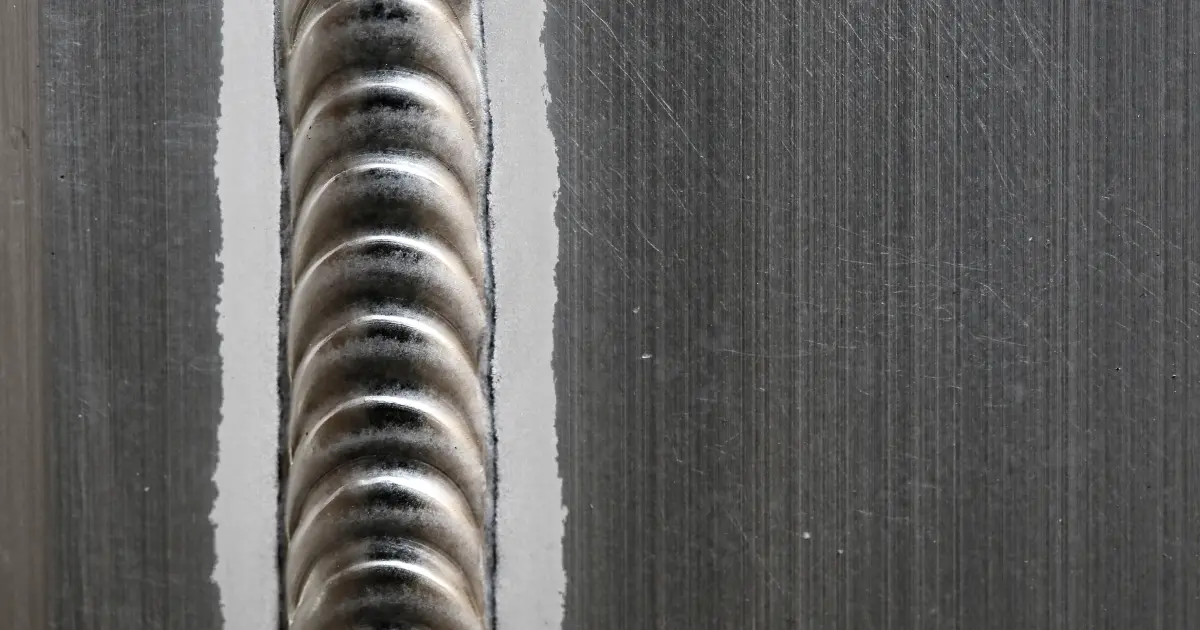
Variables Influencing Porosity Formation
The occurrence of porosity in welding is affected by a myriad of variables, varying from gas protecting efficiency to the details of welding criterion setups. One crucial aspect contributing to porosity formation is poor gas protecting. When the protecting gas, usually argon or CO2, is not effectively covering the weld pool, atmospheric gases like oxygen and nitrogen can infect the molten steel, bring about porosity. In addition, the cleanliness of the base materials plays a substantial role. Contaminants such as rust, oil, or wetness can evaporate throughout welding, developing gas pockets within the weld. Welding criteria, consisting of voltage, existing, travel rate, and electrode kind, likewise impact porosity formation. Using incorrect setups can generate excessive spatter or heat input, which subsequently can lead to porosity. The welding strategy utilized, such as gas metal arc welding (GMAW) or secured steel arc welding (SMAW), can affect porosity formation due to variations see this site in heat distribution and gas protection. Recognizing and regulating these aspects are essential for lessening porosity in welding procedures.
Results of Porosity on Weld High Quality
Porosity formation dramatically jeopardizes the architectural stability and mechanical properties of welded joints. When porosity is present in a weld, it produces spaces or tooth cavities within the product, minimizing the overall have a peek at this site strength of the joint. These voids function as anxiety focus factors, making the weld more vulnerable to breaking and failure under load. The visibility of porosity also deteriorates the weld's resistance to deterioration, as the trapped air or gases within deep spaces can react with the surrounding environment, resulting in deterioration over time. In addition, porosity can impede the weld's ability to withstand stress or effect, further threatening the general top quality and dependability of the bonded framework. In vital applications such as aerospace, automotive, or architectural building and constructions, where safety and toughness are vital, the damaging impacts of porosity on weld high quality can have severe repercussions, highlighting the value of lessening porosity with correct welding methods and treatments.
Strategies to Lessen Porosity
Additionally, using the appropriate welding parameters, such as the proper voltage, existing, and take a trip rate, is crucial in avoiding porosity. Preserving a consistent arc size and angle throughout welding additionally assists reduce the probability of porosity.

Utilizing the appropriate welding method, such as back-stepping or utilizing a weaving motion, can also help disperse warmth uniformly and reduce the possibilities of porosity formation. By applying these methods, welders can successfully lessen porosity and produce premium bonded joints.
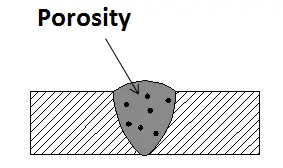
Advanced Solutions for Porosity Control
Carrying out advanced modern technologies and innovative methods plays an essential function in achieving remarkable control over porosity in welding processes. One advanced option is using innovative gas combinations. Securing gases like helium or a mix of argon and hydrogen can aid minimize porosity by offering much better arc stability and enhanced gas insurance coverage. Furthermore, employing advanced welding methods such as pulsed MIG welding or changed ambience welding can additionally assist mitigate porosity concerns.
One more advanced service entails the use of innovative welding tools. Utilizing devices with built-in functions like waveform control and sophisticated power resources go to this web-site can enhance weld high quality and minimize porosity threats. Additionally, the application of automated welding systems with exact control over specifications can significantly minimize porosity flaws.
Moreover, including advanced tracking and evaluation innovations such as real-time X-ray imaging or automated ultrasonic screening can help in identifying porosity early in the welding procedure, enabling immediate corrective actions. Overall, integrating these advanced services can greatly improve porosity control and boost the general high quality of welded elements.
Verdict
To conclude, comprehending the scientific research behind porosity in welding is vital for welders and producers to produce top quality welds. By identifying the aspects influencing porosity formation and applying techniques to minimize it, welders can boost the overall weld high quality. Advanced services for porosity control can further improve the welding procedure and guarantee a solid and trusted weld. It is essential for welders to continuously enlighten themselves on porosity and execute ideal practices to attain optimal outcomes.